CNC Milling Machines: Jot Down the Important Variations and Matching Purposes
In the world of precision manufacturing, CNC milling machines play a critical role in producing intricate parts and components across various industries. These machines use computer numerical control (CNC) to automate the milling process, ensuring high precision and repeatability. Understanding the various CNC milling machines and their purposes can help manufacturers select the right machine for their production processes.
This article explores the different types of CNC milling machines available, their key variations and the matching purposes for each. From vertical CNC milling to CNC Milling & VMC, we will break down the most important variations and how they impact the choice of equipment in specific applications.
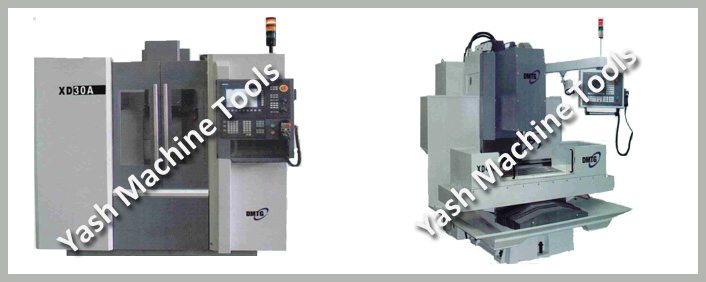
Types of CNC Milling Machines
When discussing milling machines, it’s essential to first understand the main categories of these machines. The type of milling machine selected depends on factors such as the material being worked on, the complexity of the task and the required precision.
Vertical Milling Machines
Vertical milling machines are some of the most widely used machines in the CNC world. The key characteristic is that the spindle axis is vertically oriented, meaning the cutting tool moves up and down along the material.
- Purpose: Ideal for drilling, boring and cutting slots. They are particularly effective when working with materials such as metals and plastics.
- Applications: Vertical CNC milling machines are used in industries such as aerospace, automotive and metalworking, where high precision and detailed cuts are required.
Horizontal Milling Machines
Unlike their vertical counterparts, horizontal milling machines feature a horizontal spindle orientation, meaning the tool moves in a side-to-side motion across the material.
- Purpose: Perfect for large, heavy workpieces and tasks that require the removal of larger volumes of material. Horizontal machines can accommodate more significant parts and can operate at higher speeds.
- Applications: These machines are ideal for mass production, including tasks like slot cutting, gear cutting and surface milling.

Mini Milling Machines
Mini milling machines are compact versions of larger CNC mills. These machines are designed for smaller tasks and are perfect for hobbyists, small workshops industries that need to produce smaller parts with high precision.
- Purpose: Milling machines are designed for light-duty work. They are commonly used in small-scale machining, prototyping and educational settings.
- Applications: Small businesses, model-making and prototyping are common areas where mini milling machines are used, offering both versatility and affordability.
CNC Milling & VMC (Vertical Machining Centers)
CNC Milling & VMC is a combination of milling and machining, where vertical machining centers incorporate CNC controls to perform milling, drilling and tapping operations automatically.
- Purpose: These machines are designed for high-volume, high-precision work in industries like aerospace, automotive and medical device manufacturing.
- Applications: VMCs are used for complex parts where high accuracy and tight tolerances are required. They are perfect for operations like surface grinding, high-speed machining and multi-axis machining.
Key Variations and Their Matching Purposes
Now that we have outlined the main types of CNC milling machines, it’s essential to explore their key variations and understand how each machine fits into different manufacturing processes.
Speed and Precision
One of the primary distinctions between different types of CNC milling machines is their speed and precision. For example:
- High-speed CNC milling machines are designed for rapid production and are typically used in industries requiring mass production. These machines can perform multiple operations in a short period, but they may sacrifice some degree of precision for the sake of speed.
- Precision milling machines, on the other hand, focus on accuracy and are more suitable for industries where exact measurements and tight tolerances are critical. For example, a vertical CNC milling machine used in medical device production may need to focus on precision rather than speed to ensure that parts meet the required standards.
Size and Complexity of Workpieces
The size and complexity of the workpieces being manufactured also determine which CNC milling machine is most appropriate.
- Mini milling machines are best suited for small parts with relatively simple shapes. For instance, a hobbyist might use a mini milling machine to create custom designs or models.
- Larger, industrial-scale milling machines, such as hydraulic press machines, are used for heavy-duty workpieces and can process larger components with greater force and power.
Automation and CNC Control
Automation has revolutionized CNC milling processes and the level of automation required depends on the application.
- Entry-level machines often feature manual control, offering flexibility for small-scale or manual shops where specialized tasks need to be performed.
- Fully automated CNC milling machines, feature advanced controls that can execute a series of operations automatically, significantly reducing human intervention and increasing production rates.
Material Compatibility
Different CNC milling machines are optimized for various materials, such as metals, plastics, composites or wood.
- Vertical CNC milling machines are often used for cutting harder materials like steel, aluminum and titanium due to their precision and robust design.
- Mini milling machines, are typically used for lighter materials like plastic, soft metals or composites, as these machines do not have the same load-bearing capabilities as industrial machines.
Multi-Axis Capability
Another variation that affects the choice of CNC milling machine is the number of axes the machine operates on. The number of axes available in a CNC milling machine determines the complexity of cuts it can make.
- 2-axis milling machines are generally used for simpler, flat cuts.
- 3-axis machines are commonly used for more complex shapes and cutting profiles.
- 5-axis CNC machines offer the highest level of flexibility and precision, making them ideal for the most intricate and detailed workpieces, such as in aerospace and medical applications.

Benefits of CNC Milling Machines
- High Precision: CNC milling machines offer exceptional accuracy, ensuring that each part is made according to tight tolerances. This is crucial in industries where even the smallest deviation can lead to product failure.
- Repeatability: CNC milling machines can produce identical parts in high volumes, maintaining consistency and reducing the risk of human error.
- Flexibility: With adjustable parameters and multiple tool options, CNC machines can adapt to different materials and complex designs. Whether working with metals or plastics, the right CNC machine can handle a variety of tasks.
- Efficiency: The automation and high-speed capabilities of CNC milling machines significantly increase production rates. This is particularly beneficial in industries requiring large quantities of parts to be manufactured quickly.
- Cost-Effective for Long-Term Production: While CNC milling machines can be a substantial initial investment, their ability to produce high-quality parts at scale can lead to significant cost savings in the long run.
Conclusion
Understanding the CNC milling machines available and how their different variations cater to specific purposes is crucial for selecting the right machine for your manufacturing needs. Whether you require a mini milling machine for small-scale projects or a vertical CNC milling machine for high-precision industrial tasks, knowing the advantages of each machine will help optimize production and ensure high-quality results.
The CNC milling machines all serve unique functions but are united by their ability to automate and precisely control the cutting process. By matching the appropriate machine to the required task, manufacturers can enhance efficiency, reduce material waste and improve product quality.
- Top 10 Benefits of Using TIG Welding Machines in Modern Manufacturing
- How Hydraulic Press Machine Demand and Supply Dynamics are Shaping the Market?
- How Radial Drilling Machines Achieve Low Vibration and Distortion Resistance?
- How Feed Rate Adjustments Improve Surface Finish in Vertical CNC Milling Machines?
- How Chamfer Machines Are Streamlining Metalwork in the UK’s Manufacturing Sector?
- How Lathe Machine Manufacturers are Powering the Nation’s Engineering Growth in Canada?