Mig Welding Machine – Important Things to Consider When Using
In order to make your life easier when using a Mig Welding Machine, here are some important things to consider. These factors include 125 amps, flux cored wire, four transfer modes, and shielding gas requirements. Hopefully, this article has helped you make a better decision. We will discuss each of these points and how they can affect the quality of your work. Make sure to read through these tips and be sure to purchase the best Mig Welding Machine for your specific needs.
Mig Welding Machine 125 Amps
When determining how much power you need from a Mig welding machine, the amount of wire feed speed will be a critical factor. Check the manual for specific parameters, such as wire feed speed. Wire feed speed is a critical control on the amperage and amount of weld penetration. Increase the wire feed speed as the welder’s power increases, but be careful not to use too much wire feed speed, or you could end up burning the piece.
Choose a wire size that falls in the middle of the amperage range of the wire diameter. Wire diameters are often listed on the wire data sheet, as the chart shows. The wire feed speed is calculated in inches per minute, and the amperage setting is dependent on the wire size and the material thickness. To select the correct amperage setting for your machine, consult the manual or weld specification sheet.
Flux Cored Wire for Mig Welding Machine
There are some advantages and disadvantages to using flux cored wire for your Mig welding machine. For one, it requires more materials and can be a more expensive option. However, flux cored wire also has many advantages such as reduced material consumption, easy installation, and reduced production time. In this article, we will compare both types of wire and their advantages. Read on to learn more. Welding with flux cored wire will save you time and money!
It can also save you money as you won’t need to purchase shielding gas. This is because the wire’s core contains ingredients that shield the weld pool from contaminants. In addition, it can also save you time because you won’t have to change the shielding gas during welding. However, it is important to note that it is not recommended for welding outdoors because a stiff breeze may disperse the gas and make it ineffective.
Four Transfer Modes of Mig Welding Machine
There are four basic types of transfer modes for mig welding machines. Each mode has a unique set of parameters and a unique effect on the metal. The globular mode transfers metal in irregular globs, which are larger than the diameter of the electrode. These globs are ideal for welding thinner materials and are less easily controllable in horizontal positions. The arc-stabilizing gas mixture is also critical to globular transfer mode.
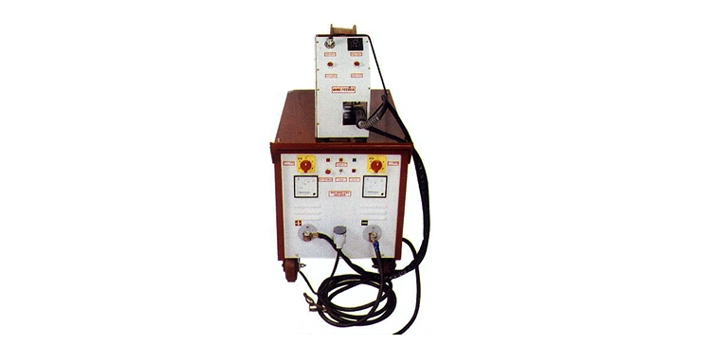
The globular transfer mode is similar to the uncontrolled short-circuit/dip mode, but the wire voltage remains higher than the dip range. The result is large drops of molten metal that are carried to the workpiece by gravity. This transfer mode is primarily used on carbon steel and is limited to flat positions. Because it does not produce a smooth wed bead finish, it’s not recommended for welded items with a lot of rounded edges. Additionally, substantial spatter can occur with this transfer mode.
Shielding Gases for Mig Welding Machine
When it comes to choosing the right shielding gas for your Mig welding machine, you have several options to choose from. You should choose the gas based on the type of metal and thickness, as well as on your preferences for weld penetration and time limit. To learn more, check out the following Shielding Gas Chart. It’ll help you make the right choice. Once you’ve chosen the right gas, you’ll be ready to get started on your welding project!
First, consider what metal you are welding. Choose the shielding gas that matches the base material. Most welding procedure specifications specify the gas mix for each filler metal. Also, think about the type of transfer mode you’re using. You might be using a spray transfer mode, which pairs better with a particular type of shielding gas. Using a mixture of 90 percent argon with 10 percent carbon dioxide for spray transfers is better, though CO2 levels should not exceed 25 percent.
- How Lathe Machine Manufacturers are Powering the Nation’s Engineering Growth in Canada?
- How Chamfer Machines Are Streamlining Metalwork in the UK’s Manufacturing Sector?
- How Feed Rate Adjustments Improve Surface Finish in Vertical CNC Milling Machines?
- How Radial Drilling Machines Achieve Low Vibration and Distortion Resistance?
- From Design to Execution: How CNC Press Brakes Ensure Seamless Workflow
- How to Optimize Sheet Metal Operations Using a Hydraulic Press Brake?