CNC Press Brake: Precision Bending for Modern Manufacturing
In the world of metal fabrication, precision, efficiency, and versatility are essential for success. One machine that plays a pivotal role in shaping metal components with high accuracy and consistency is the CNC Press Brake. Known for its ability to bend sheet metal into precise angles and shapes, the CNC press brake is an essential tool in industries ranging from automotive and aerospace to electronics and construction.
In this article, we will explore the various aspects of CNC press brakes, including their design, working principles, key features, types, advantages, and applications. We will also examine how CNC press brakes have revolutionized metalworking processes by enhancing precision, reducing setup times, and offering greater control over complex bending operations.
What is a CNC Press Brake?
A CNC press brake is a computer-controlled machine used to bend and shape metal sheets into predefined shapes and angles. “CNC” stands for Computer Numerical Control, which means that the machine is programmed to perform precise bending operations based on digital instructions. Unlike traditional manual press brakes, CNC press brakes use software to control the movement of the ram and the back gauge, allowing for highly accurate and repeatable bending operations.
The main components of a CNC press brake include the ram, which holds the upper die and moves vertically to apply pressure on the workpiece, and the bed, which holds the lower die and supports the sheet metal. The combination of the upper and lower dies determines the shape and angle of the bend. The CNC system controls the position of the ram and back gauge, ensuring that the metal is bent precisely to the desired specifications.
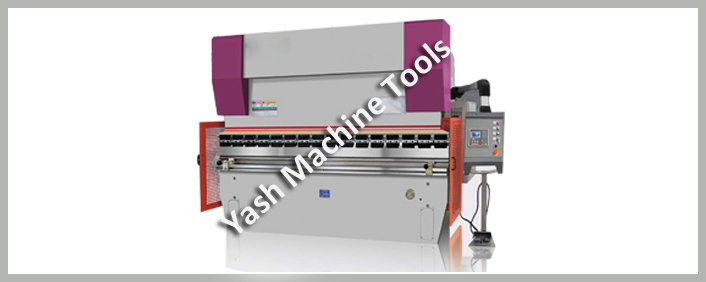
Working Principle of a CNC Press Brake
The operation of a CNC press brake is based on the principle of controlled deformation. When the ram presses the metal sheet between the upper and lower dies, the material is forced to bend. The CNC system controls the movement of the ram and back gauge to ensure that the bend angle, depth, and position are accurate.
Here’s a step-by-step overview of how a CNC press brake works:
- Loading the Metal Sheet: The operator places the metal sheet onto the bed of the press brake. The sheet is aligned with the back gauge, which is controlled by the CNC system.
- Programming: The operator inputs the bending parameters into the CNC controller, including the bend angle, position, and the number of bends required. This data is converted into digital instructions that control the movement of the ram and back gauge.
- Bending: Once the program is set, the ram moves downwards, pressing the metal sheet between the dies. The pressure applied by the ram forces the sheet to bend to the desired angle.
- Multiple Bends: If multiple bends are needed, the CNC system automatically adjusts the position of the back gauge, allowing the sheet to be repositioned for the next bend without manual intervention.
- Final Output: Once the bending process is complete, the CNC press brake produces a precisely bent metal component that matches the programmed specifications.
Key Features of a CNC Press Brake
CNC press brakes are designed with advanced features that make them highly efficient and precise for modern manufacturing needs. Some of the key features include:
- CNC Controller: The CNC controller is the brain of the press brake, allowing operators to program complex bending sequences with high precision. The controller calculates the bending angle, back gauge position, and ram movement, ensuring accurate and repeatable results.
- Back Gauge: The back gauge is an adjustable device that positions the metal sheet at the correct distance from the dies. The CNC system automatically adjusts the back gauge to ensure the sheet is positioned correctly for each bend, making the process faster and more precise.
- Hydraulic or Electric Drive Systems: CNC press brakes can be powered by hydraulic or electric systems. Hydraulic press brakes offer high force for heavy-duty applications, while electric press brakes provide faster speeds and greater energy efficiency.
- Precision Tooling: CNC press brakes use interchangeable upper and lower dies to create different bend profiles. Precision tooling ensures that the bends are consistent, even for complex shapes and angles.
- Multiple Axis Control: Advanced CNC press brakes offer control over multiple axes, allowing for more complex bending operations. For example, the machine can control the position of the ram, the back gauge, and side supports, enabling the creation of intricate components with multiple bends.
- Automatic Crowning: Crowning is a technique used to compensate for deflection in the press brake’s bed or ram during the bending process. CNC press brakes often include automatic crowning systems that adjust the bed or ram to ensure uniform bending across the entire length of the workpiece.
- User-Friendly Interface: Modern CNC press brakes come equipped with intuitive touch-screen interfaces, making it easy for operators to program and monitor the bending process. This reduces the learning curve and allows operators to perform complex bending operations with ease.

Types of CNC Press Brakes
CNC press brakes come in several different types, each suited for specific applications and industries:
1. Hydraulic CNC Press Brake:
Hydraulic CNC press brakes are driven by hydraulic cylinders that provide high pressure and force for bending thick and heavy materials. These machines are ideal for applications that require significant bending force, such as the fabrication of large metal components.
2. Electric CNC Press Brake:
Electric CNC press brakes use electric motors to drive the ram, offering greater precision and faster operation compared to hydraulic models. They are energy-efficient and are best suited for applications that require high-speed production and accuracy, such as the electronics and automotive industries.
3. Hybrid CNC Press Brake:
Hybrid CNC press brakes combine the benefits of both hydraulic and electric systems. They offer high power for heavy-duty bending while providing the energy efficiency and precision of electric drives.
4. Servo-Driven CNC Press Brake:
Servo-driven CNC press brakes use servo motors to control the movement of the ram and back gauge, providing exceptional control over the bending process. These machines are known for their high precision and repeatability, making them ideal for industries that require tight tolerances.
Advantages of CNC Press Brakes
CNC press brakes offer several advantages over traditional manual press brakes, making them a preferred choice in modern metalworking and manufacturing:
1. High Precision:
CNC press brakes are known for their ability to produce highly accurate bends, even in complex shapes. The CNC controller ensures that each bend is executed to the exact specifications, minimizing errors and material wastage.
2. Increased Productivity:
The automation provided by the CNC system allows for faster setup times, reduced manual labor, and higher production speeds. Multiple bends can be performed in a single setup, improving overall efficiency.
3. Repeatability:
Once a bending program is saved, it can be reused for future jobs, ensuring consistent results every time. This repeatability is particularly valuable for mass production and batch processing.
4. Reduced Material Waste:
CNC press brakes minimize the risk of human error, reducing the amount of material wasted due to incorrect bends. The precision of CNC programming ensures that each piece is bent correctly the first time.
5. Versatility:
CNC press brakes can handle a wide range of materials and thicknesses, from thin aluminum sheets to thick steel plates. The versatility of the machine makes it suitable for various industries and applications.
6. Complex Bending Operations:
CNC press brakes are capable of performing complex bending operations, including multi-axis bending, hemming, and offset bending. This capability opens up new possibilities for creating intricate components with precision.
Applications of CNC Press Brakes
CNC press brakes are widely used across various industries for their ability to produce precise metal components. Some common applications include:
- Automotive Manufacturing: CNC press brakes are used to produce parts such as body panels, chassis components, and brackets for vehicles.
- Aerospace Industry: These machines are used to fabricate structural components for aircraft, including wings, fuselage parts, and engine components.
- Electronics Industry: CNC press brakes are used to create enclosures, brackets, and connectors for electronic devices.
- Construction: Press brakes are used to fabricate metal components for buildings, bridges, and infrastructure projects.
- Metal Fabrication: CNC press brakes are essential for custom metal fabrication, including creating parts for machinery, appliances, and equipment.
Conclusion
The CNC Press Brake is a powerful and versatile machine that has transformed the way industries approach metal bending and fabrication. Its ability to produce highly accurate bends with minimal manual intervention makes it a vital tool in modern manufacturing. Whether used for large-scale production or intricate custom projects, CNC press brakes offer the precision, efficiency, and versatility needed to meet the demands of today’s competitive industrial landscape.
Investing in a CNC press brake allows manufacturers to streamline their operations, reduce material waste, and ensure the highest level of precision, making it an indispensable asset in any metalworking facility.
- How Lathe Machine Manufacturers are Powering the Nation’s Engineering Growth in Canada?
- How Chamfer Machines Are Streamlining Metalwork in the UK’s Manufacturing Sector?
- How Feed Rate Adjustments Improve Surface Finish in Vertical CNC Milling Machines?
- How Radial Drilling Machines Achieve Low Vibration and Distortion Resistance?
- From Design to Execution: How CNC Press Brakes Ensure Seamless Workflow
- How to Optimize Sheet Metal Operations Using a Hydraulic Press Brake?