Buying a TIG Welding Machine
Getting the right TIG welding machine is an important step to make sure your welding job is as productive as possible. There are a few things to look out for when you are shopping for one of these machines.
What Should be the Arc Length of TIG Welding Machine?
Choosing the correct arc length is an important factor in producing a quality weld. A long arc may not produce the best results and a short arc may cause a faulty weld.
If you have not already done so, you should check the machine settings for heat before you begin welding. It is possible to run a welding machine on too little gas or too little current. A sloppy weld will cause the fusion of the metal to break down.
The arc may be too short, too long, or too much of the same. Arc length is also affected by the angle of the torch. For instance, a long arc may not produce the best results when making a horizontal fillet weld.
It is also possible to do a poor job of welding by choosing the wrong electrode angle. For instance, if you are welding a vertical joint, the electrode should be perpendicular to the line of weld. However, this will not work in all situations.
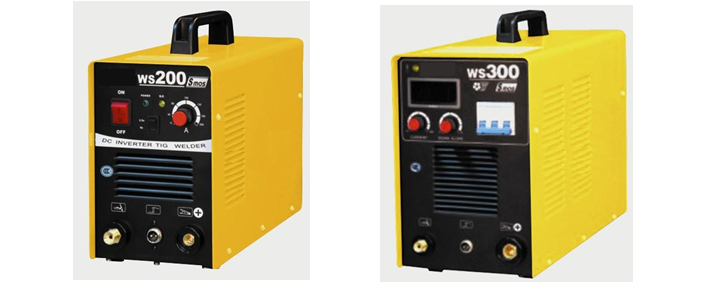
How to Choose the Gas Flow Rate in TIG Welding Machine?
Choosing the right gas flow rate is a daunting task. The wrong shielding gas flow can lead to weld quality issues and an increase in costs. It can also lead to hazardous safety problems.
It is important to choose the right shielding gas for your tig welding machine. If you use the wrong gas, you may end up with a messy weld that leaves black soot and porosity. It can also increase your cost of doing business.
Choosing the right gas flow rate is crucial for any welding environment. The incorrect rate can lead to wasted gas and downtime. The right flow rate can prevent these problems and improve the quality of your welded joint.
There are several factors that determine the correct flow rate. In the beginning stages of your weld, you should be aware of the minimum and maximum flow rates for your particular machine.
The optimal gas flow rate for your TIG welding machine will depend on several factors. For example, if you are welding wide joints, you may want to increase your shielding gas flow rate to improve coverage.
Tungsten is a Metal Used in Tig Welding
Choosing the right Tungsten electrode is one of the most important components of a successful TIG welding process. The quality of the welding arc can be directly influenced by the type and shape of the electrode, as well as by the machine, operator, and other factors.
Depending on the weld job, the shape and size of the electrode should be matched with the material to be welded. This allows for improved welding performance and saves time and effort.
Tungsten electrodes come in different shapes, sizes, and compositions. They are available as pure tungsten, rare earth alloys, and color-coated. Each type has its own advantages and disadvantages.
Using a rare-earth tungsten electrode improves the stability of the arc and increases the longevity of the electrode. In addition, these electrodes are better for AC welding. They also have better ignition rates. Compared to pure tungsten, these electrodes may sustain a faster arc start.
Tungsten is used as an electrode in both AC and DC welding applications. These electrodes are able to handle the power of the welding process without melting. This means that they can be used with thin sheet metal and other workpieces that may be difficult to weld.
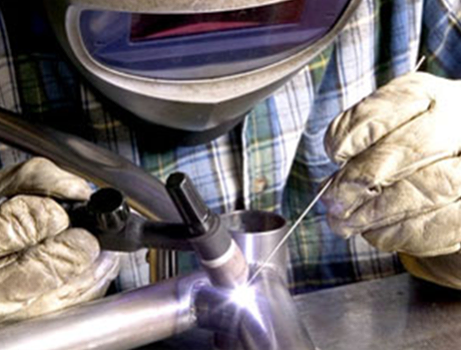
The Bottom Line to Benefits of TIG Welding Machine
Whether you’re a seasoned professional or just getting started, learning the difference between TIG welding and MIG welding can help you find the right method for your project. Both are effective at creating strong welds, but they can vary in the way they are applied.
While MIG welding is easy to learn, TIG requires a bit more preparation and skill. A good weld requires a balanced blend of electrical current, filler material addition rate, and puddle speed. If you don’t do it right, you’ll end up with weak welds.
TIG welding is more expensive than MIG, but it does offer several advantages. It creates a more precise weld that’s less prone to spatter. It also provides a strong, clean joint.
It’s also easier to use and is less messy. It’s best for bigger projects and professional welders. But it requires more time and hood time. You’ll need several hundred hours of hood time to master the TIG process.
Both weld types can be used on a wide range of materials. However, TIG welding is better for thinner metals, such as aluminum, and produces more accurate penetration.
- How Radial Drilling Machines Achieve Low Vibration and Distortion Resistance?
- How Feed Rate Adjustments Improve Surface Finish in Vertical CNC Milling Machines?
- How Chamfer Machines Are Streamlining Metalwork in the UK’s Manufacturing Sector?
- How Lathe Machine Manufacturers are Powering the Nation’s Engineering Growth in Canada?
- From Design to Execution: How CNC Press Brakes Ensure Seamless Workflow
- How to Optimize Sheet Metal Operations Using a Hydraulic Press Brake?