Advancements in Vertical Milling Machine Technology
The latest innovations in vertical milling machine technology are making these machines more versatile and accurate. These changes help manufacturers complete their projects faster and more efficiently. In addition, they allow us to work on different surfaces and sizes. This helps them reduce the need for additional fixtures and tools.
High-Speed Spindles and Their Role in Precision Machining
The High-Speed Spindle is one of the key components of a milling machine. It contains the motor that controls revolutions, power and torque, as well as the tool axis that holds the cutting tools.
The spindle also includes the clamping mechanism that secures the tools in place. There are several types of spindles, including swivel head spindles and vertical-style spindles that allow the machine to perform certain operations at angles.
Another important component of the spindle is its bearings. They help keep the tools secure and protect the workpiece. A high-speed spindle is a great option for machining jobs that need more speed than a standard machine tool’s spindle can provide. These spindles are designed to increase the machine’s RPM while ensuring the highest level of precision and reliability. High-speed spindles are available for a variety of machine tool models and sizes. They can be integrated into the machine’s existing spindle to increase the RPM without modifying it.
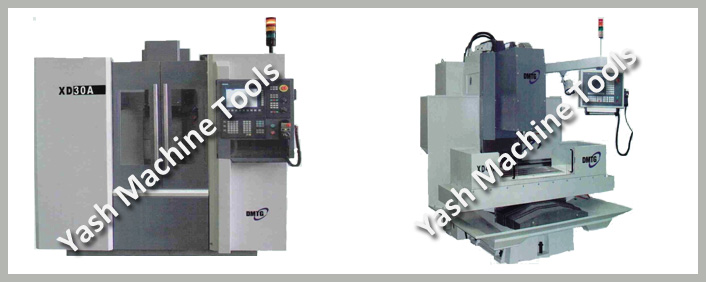
The Vital Role of CNC Controls in Milling Machines
CNC controls are a critical component in the manufacturing process because they ensure accuracy, consistency, and precision. They also allow for a variety of different machine tools to be used in one cell.
The controls for a CNC milling machine can vary greatly depending on the specific machine. The most common controls include a programmable controller that accepts input from the operator and launches a program to execute the required milling operation.
The High-Speed Tool Change is a process that increases machining speed using tools that are faster and more accurate. The technology uses a milling cutter with multiple cutting edges that remove material from a workpiece with each pass of the tool.
This is a major advance in manufacturing efficiency. Previously, manual machines required a lot of setup and changeover to machine a new part, but CNC machining centres with automatic tool changers.
The technology is used in the vertical machining centre segment of the industry, which provides increased operating flexibility due to a range of customization options, like static palletization systems and mobile pallet changing systems. These technologies can help reduce the production preparation and trial manufacturing cycle, as well as improve the quality of finished parts.
High-Speed Cutter Feed in Milling Machine
The high-speed cutter feed is one of the most important cutting variables for achieving precision in milling. It varies based on the tool diameter, operation, material, etc. The speed of the tool removes material by performing many small cuts in a time period. This removes a lot of material faster than using a single large cut.
It also has a significant impact on the surface roughness of a finished part. It can cause scallop marks, scratches, or micro pits. Depending on the cutter diameter, feed rate, and surface roughness, these can have different impacts on the appearance of the finished part.
Revolution ridges are the characteristic finish of face milling operations. They appear as trochoidal marks following the movement of points on the cutter’s end face and are a result of the rapid feed rate used in this type of work.
- How Lathe Machine Manufacturers are Powering the Nation’s Engineering Growth in Canada?
- How Chamfer Machines Are Streamlining Metalwork in the UK’s Manufacturing Sector?
- How Feed Rate Adjustments Improve Surface Finish in Vertical CNC Milling Machines?
- How Radial Drilling Machines Achieve Low Vibration and Distortion Resistance?
- From Design to Execution: How CNC Press Brakes Ensure Seamless Workflow
- How to Optimize Sheet Metal Operations Using a Hydraulic Press Brake?