Why Precision is a Priority: The Role of Mechanical Stops and Steel Torsion Bars in Hydraulic Press Brakes
In the world of metal fabrication, precision plays a crucial role in ensuring that parts are accurately formed to the required specifications. When working with hydraulic press brakes, maintaining high precision is essential for achieving quality bends and shapes without compromising material integrity. The ability of a press brake machine to maintain this precision is directly influenced by the mechanical stops and steel torsion bars that are integral to its design. These components work in tandem to control the movement of the ram, which is a pivotal part of the bending process.
This article delves into the role that mechanical stops and steel torsion bars play in enhancing the performance and accuracy of a hydraulic press brake. By understanding their functions, operators can optimize the capabilities of their machines, leading to more consistent results and a higher standard of quality in their finished products.
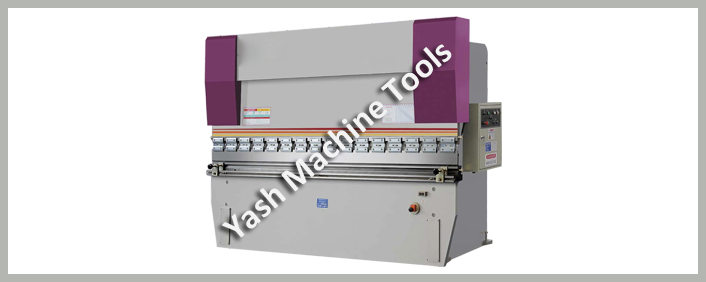
The Role of Mechanical Stops in Hydraulic Press Brakes
Mechanical stops are critical components in hydraulic press brakes that ensure the precise positioning of the ram during the bending process. They act as a limit or “stop” that prevents the ram from moving too far during its stroke. Without properly functioning mechanical stops, the ram could travel beyond the desired point, resulting in inconsistent bends or damage to the material being worked on.
How Mechanical Stops Improve Precision
- Position Control: Mechanical stops are used to control the stroke length of the ram in a press brake. By adjusting the stops, operators can set the ram’s travel to a specific depth, ensuring uniformity across the entire batch of bends.
- Minimizing Error: By preventing the ram from over-traveling or under-traveling, mechanical stops significantly reduce human error and machine inaccuracies. This consistency is crucial for producing high-quality bends that meet exact specifications.
- Compensation for Wear: Over time, wear and tear can affect the performance of the hydraulic press brake. Mechanical stops can be adjusted to compensate for any minor shifts in the system, ensuring that the machine continues to produce precise results even after extensive use.

Types of Mechanical Stops
- Manual Stops: These are typically adjusted by the operator to set the desired depth for the ram. While they provide flexibility, they can be prone to slight inaccuracies due to human error or inconsistent adjustments.
- Electrical Stops: These provide more precise control by utilizing electrical systems to automatically set and adjust the ram position. Electrical stops are ideal for applications where high repeatability and accuracy are required.
- Digital Stops: A more advanced version of electrical stops, digital systems offer real-time feedback and adjustments based on a digital display, which ensures that the hydraulic press brake operates with extreme precision.
In combination with steel torsion bars, mechanical stops ensure that the press brake can produce bends with exact angles, minimal deviation and high repeatability, even with different materials and thicknesses.
Steel Torsion Bars: The Backbone of Precision in Press Brakes
Steel torsion bars are an essential element in press brakes, serving as the primary force transmission mechanism between the machine’s hydraulic system and the ram. These bars work by applying torque, which is critical in the bending process. Their role in maintaining precision stems from their ability to evenly distribute force and maintain synchronization between different parts of the machine.
How Steel Torsion Bars Improve Precision
- Torque Distribution: The primary function of a steel torsion bar is to evenly distribute the force applied by the hydraulic system across the machine’s components. By doing so, it ensures that the ram remains aligned throughout its stroke, reducing the risk of skewed or uneven bends.
- Maintaining Synchronization: Torsion bars help synchronize the motion of the upper and lower beams of the press brake. This synchronization is crucial in preventing any misalignment between the punch and the die, ensuring that the material is bent evenly across its entire length.
- High Precision and Stability: Steel torsion bars provide a high level of precision by minimizing deflection and vibration during the bending process. Their robust design allows them to absorb and dissipate forces, ensuring that the press brake machine operates smoothly without compromising accuracy.
Benefits of Steel Torsion Bars in Hydraulic Press Brakes
- Increased Load-Bearing Capacity: Steel torsion bars are designed to withstand heavy loads, making them ideal for bending thicker materials. This ability to handle increased force without compromising on precision is one of the key advantages of hydraulic press equipped with torsion bars.
- Durability and Longevity: Steel torsion bars are built to last. Their resistance to fatigue means that they can handle repeated use over long periods without experiencing significant wear, contributing to the overall longevity of the press brake machine.
- Enhanced Consistency: By minimizing deflection and mechanical slippage, steel torsion bars ensure that the hydraulic press brake machine maintains consistent performance. This consistency is vital for industries where tight tolerances are required, such as aerospace or automotive manufacturing.
Integrating Mechanical Stops and Steel Torsion Bars for Optimal Performance
When used together, mechanical stops and steel torsion bars work in harmony to provide the highest level of precision in hydraulic bending operations. While mechanical stops control the stroke and prevent errors, steel torsion bars ensure that the force is evenly distributed and that the machine operates with minimal deflection.
Synchronization and High Precision
The synergy between mechanical stops and steel torsion bars is crucial for hydraulic press brakes operating at high speeds and under heavy loads. The combination of torque distribution and precise ram positioning allows the machine to produce high-quality bends with tight tolerances. This synchronization is especially important in high-volume production environments where repeatability and consistency are key.

Reducing Setup Times and Improving Productivity
By utilizing press brakes with finely tuned mechanical stops and high-quality steel torsion bars, manufacturers can reduce setup times, minimize material waste and enhance the overall throughput of the production process. These improvements in efficiency not only boost productivity but also reduce the need for costly adjustments or rework.
Conclusion
In the competitive world of metal fabrication, precision is a priority. The hydraulic press brake, with its mechanical stops and steel torsion bars, ensures that every bend is accurate, consistent and high-quality. These components work together to provide the necessary synchronization and force distribution required for efficient bending operations. By maintaining the integrity of the machine’s movements and reducing wear, these elements play a vital role in extending the lifespan of the press brake machine and improving its overall performance.
Manufacturers can achieve greater accuracy, reduce downtime and increase productivity by investing in hydraulic press brakes with properly integrated mechanical stops and steel torsion bars. Whether using any machine, understanding the significance of these components is crucial for maintaining the machine’s precision and reliability over time.
- Top 10 Benefits of Using TIG Welding Machines in Modern Manufacturing
- How Hydraulic Press Machine Demand and Supply Dynamics are Shaping the Market?
- How Radial Drilling Machines Achieve Low Vibration and Distortion Resistance?
- How Feed Rate Adjustments Improve Surface Finish in Vertical CNC Milling Machines?
- How Chamfer Machines Are Streamlining Metalwork in the UK’s Manufacturing Sector?
- How Lathe Machine Manufacturers are Powering the Nation’s Engineering Growth in Canada?