How Vibration Stress Relief, Pressing Force and Reciprocating Blade Motion Improve Hydraulic Shearing Machines?
In the realm of industrial manufacturing, shearing machines play a critical role in cutting materials with precision. These machines, are indispensable for high-performance cutting tasks in various industries, including metal fabrication, automotive and aerospace. With advancements in technology, vibration stress relief, pressing force and reciprocating blade motion have become integral elements in enhancing the performance and longevity of hydraulic shearing machines. Understanding how these factors influence machine efficiency can guide operators and manufacturers toward optimizing their systems for better results.
This guide explores how vibration stress relief, pressing force and reciprocating blade motion improve the operation of hydraulic shearing machines. By delving into the technical aspects of these features, we will highlight their role in enhancing cutting accuracy, reducing wear and increasing operational efficiency.
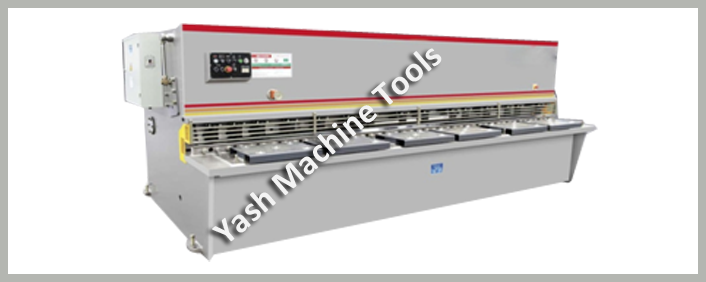
Vibration Stress Relief and Its Role in Improving Hydraulic Shearing Machines
Vibration is an inherent byproduct of any machine operation. In the context of hydraulic shearing machines, vibrations can negatively impact cutting precision and the durability of key components. Excessive vibration can cause wear and tear on parts like the CNC guillotine shearing machine’s blades, frame and hydraulic system, ultimately affecting performance and longevity.
How Vibration Affects Shearing Machines?
- Accuracy: Vibrations can lead to misalignment of the cutting blades, resulting in inaccurate cuts and uneven material edges.
- Fatigue: Continuous exposure to vibration stresses can cause metal fatigue in critical machine components, leading to premature failure.
- Surface Quality: Vibrations during the shearing process can affect the surface finish of the cut material, causing unwanted roughness.

Vibration Stress Relief Techniques
- Damping Systems: Incorporating damping systems in the machine’s frame and hydraulic components can absorb vibrations and prevent them from affecting the cutting process. These systems use materials or technologies that reduce the amplitude of vibrations.
- Balanced Design: The frame and structure of hydraulic swing beam shearing machines can be designed with better balance to distribute forces evenly, reducing vibration-induced stress.
- Precision Components: Ensuring that all moving parts, such as the blades and hydraulic components, are precision-engineered minimizes vibrations during operation.
By addressing vibration issues, manufacturers can significantly enhance the cutting precision and operational efficiency of their shearing machines.
Pressing Force: Maximizing Shearing Power
The pressing force applied by the shearing machine is a critical factor in determining its cutting ability. For CNC guillotine shearing machines, the pressing force is delivered by hydraulic systems that generate the necessary pressure to shear through various materials. The force must be calibrated to suit different materials, thicknesses and cutting angles to achieve optimal results.
Importance of Pressing Force in Shearing Machines
- Material Type and Thickness: Different materials require different amounts of force for cutting. Metals like aluminum or mild steel may require less force than harder materials such as stainless steel or titanium.
- Cutting Precision: Inadequate pressing force can lead to incomplete cuts or uneven edges, while excessive force may cause material deformation or damage.
- Tool Longevity: Properly balanced pressing force ensures that both the blades and the hydraulic system experience less stress, prolonging the life of the components.
Optimizing Pressing Force
- Adjustable Hydraulic Pressure: Modern shearing machines allow operators to adjust the hydraulic pressure according to the material being processed. This flexibility ensures that the machine operates efficiently across a variety of materials.
- Force Control Systems: Advanced force control systems enable the machine to adapt dynamically during the cutting process. These systems continuously adjust the force applied based on real-time feedback from the material being cut, ensuring consistent performance.
- Regular Maintenance: Ensuring that the hydraulic system is regularly serviced helps maintain optimal pressure levels and prevents issues such as leaks, which can reduce the pressing force.
By fine-tuning the pressing force, manufacturers can improve cutting accuracy, reduce waste and extend the life of the machine.

Reciprocating Blade Motion: Enhancing Cutting Efficiency
The motion of the shearing blade plays a significant role in the overall performance of the machine. Reciprocating blade motion refers to the back-and-forth movement of the blade as it cuts through the material. This motion is typically powered by hydraulic systems in hydraulic guillotine shearing machines.
How Reciprocating Motion Affects Shearing Machines
- Cutting Speed and Efficiency: The speed at which the blade moves directly impacts the cutting cycle time. Faster reciprocation can increase throughput, while slower motion may improve accuracy for more complex cuts.
- Load Distribution: The reciprocating motion of the blade ensures that the load is evenly distributed across the cutting edge, reducing wear and improving tool life.
- Material Shearing: The cutting action of the reciprocating blade must match the material’s hardness and thickness. Too fast of a motion can cause excessive force on the material, leading to poor cuts, while too slow of a motion may result in a loss of cutting precision.
Improving Reciprocating Blade Motion
- Optimized Blade Speed: Modern machines often feature programmable blade speed control, which allows for adjustments based on the material type and thickness. This feature ensures that the machine adapts to varying operational conditions.
- Hydraulic Systems: Advanced hydraulic systems can provide smooth, consistent reciprocating motion, ensuring minimal vibrations and wear on the machine. These systems should be well-maintained to prevent issues such as jerky blade movements, which can reduce cutting accuracy.
- Blade Design: The design of the reciprocating blade itself is crucial in maintaining cutting efficiency. High-quality, sharp blades reduce friction and require less power to cut through materials, which also reduces the load on the machine’s hydraulic system.
By optimizing reciprocating blade motion, manufacturers can improve cutting accuracy, increase productivity and reduce energy consumption.
Conclusion
In hydraulic shearing machines, particularly hydraulic guillotine shearing machines, vibration stress relief, pressing force and reciprocating blade motion play vital roles in improving performance and longevity. Vibration control techniques ensure cutting precision, while properly calibrated pressing force enhances cutting power without damaging the material or machine components. Additionally, optimized reciprocating blade motion boosts cutting efficiency and prolongs the life of the machine.
For manufacturers, understanding and optimizing these factors is essential for maximizing productivity, minimizing downtime and ensuring the highest quality cuts. Whether using shearing machine, integrating these techniques can significantly improve the performance and durability of the machine, making it an invaluable asset in any industrial setting.
- Top 10 Benefits of Using TIG Welding Machines in Modern Manufacturing
- How Hydraulic Press Machine Demand and Supply Dynamics are Shaping the Market?
- How Radial Drilling Machines Achieve Low Vibration and Distortion Resistance?
- How Feed Rate Adjustments Improve Surface Finish in Vertical CNC Milling Machines?
- How Chamfer Machines Are Streamlining Metalwork in the UK’s Manufacturing Sector?
- How Lathe Machine Manufacturers are Powering the Nation’s Engineering Growth in Canada?